What is cold plates (water- cooled heat sink)?
High-end applications, such as electronic components used in high temperature environments, require an efficient cooling system that does not interfere with operation.
Cold plates (also known as water-cooled heat sinks) are used , as the most efficient cooling method, in vacuum chambers of vapor deposition equipment in the display manufacturing process and protect electronic components from temperature environments of hundreds of degrees Celsius and thus provide a high level of performance and reliability to the equipment accordingly.
The cold plate with a water-cooled jacket structure heated in the vacuum chamber comes into contact with the cooling water circulating inside through a tube or passage (groove), which results in the entire cold plate being cooled, reducing the heat load by dissipating excess heat.
Cold plate of Kyoyu -SEISAKUSHO
Kyoyu Seisakusho’s cold plate has a water-cooled jacket structure made of aluminum, stainless steel and copper.
The method of joining the plate body and the water-cooled lid in the water-cooled jacket is specialised in Tig welding for stainless steel and friction stirring welding (FSW) for copper and aluminum. In addition, with advanced distortion technology, the ground contact with the heat source realises the optimal flatness and contributes to the improvement of cooling efficiency.
Production range
Material | Aluminum, Stainless steel, Copper |
---|---|
Joining methods | Tig welding, Vacuum brazing, Electron beam welding (EBW), Friction stirring welding (FSW) |
Maximum size that can be manufactured | Circular form:φ800mm Rectangular form:Width 1,000 mm、Length 2,000 mm |
Structure | The jacket structure having grooves covering the lid from the above is main. |
Shape | Compatible with various external shapes and complex waterway shapes |
Specifications | All manufactured parts are custom-made with customer specifications |
Product examples
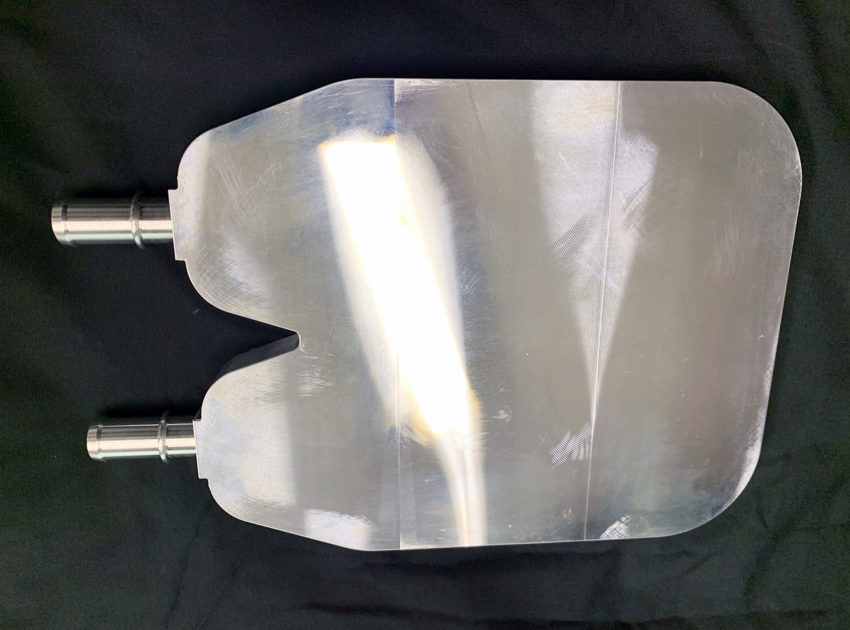
Aluminum Cold Plate (Prototype development case)
This case is a prototype development product that has been requested through the homepage. The water-cooled groove is processed into the main body, the lid is attached from the top, and then joined by FSW After joining with frictional stirring welding, the surface in contact with the heat source provides plane accuracy by machining The ...
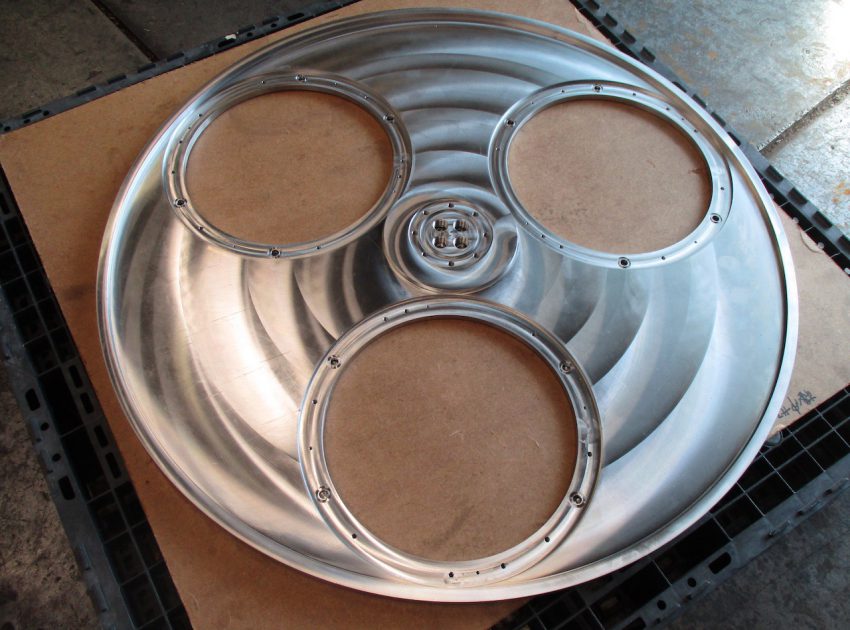
Stainless Steel Cold Plate (circular shape)
After Tig welding with a water-cooled lid to the main body, distortion correction and machine finishing are performed. After that, the distortion correction is done again to get flatness. Material SUS304 , SUS316 Size Diameter 400mm~900mm Industry Vacuum Industry Processing details Machining Center, Tig Welding
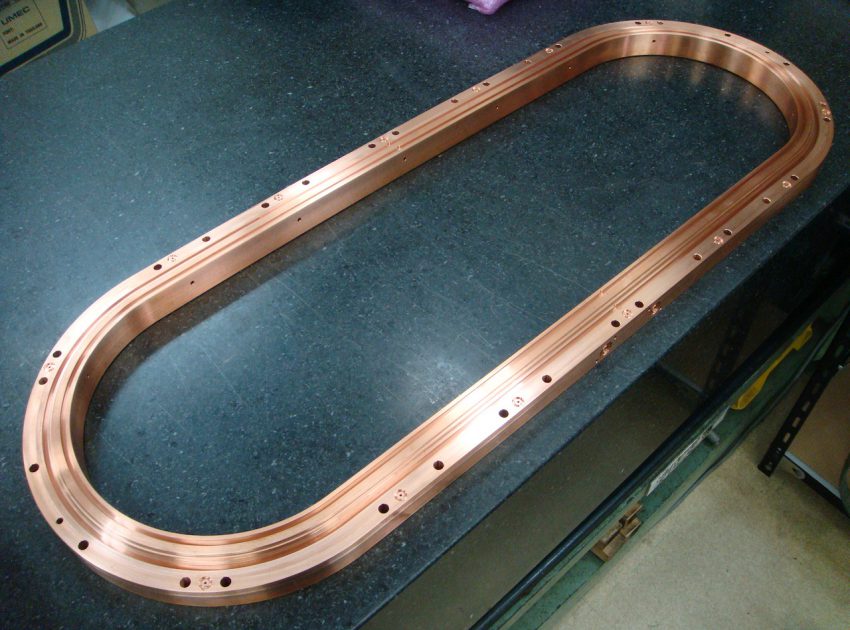
Pure Copper Cold Plate (Oval shape)
Pure copper is a difficult material, and warping occurs after cutting or joining. Therefore, in order to ensure the thickness of the water-cooled lid, distortion correction is necessary each time.It is also easy to scratch, so you need to pay close attention Material Pure Copper C1020 Size W300mm~400mm x L1000mm~1500mm Industry Vacuum Industry Processing details ...
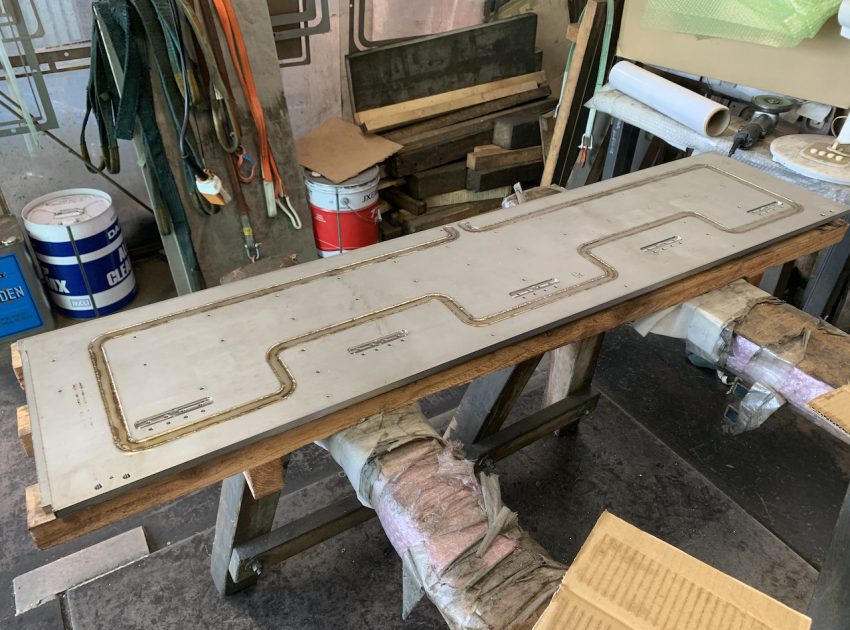
Stainless Steel Cold Plate (rectangular shape)
After Tig welding with a water-cooled lid on the main body, the distortion correction is performed to get flatness. Material SUS304、SUS316 Size W200mm~400mm x L500mm~1500mm Industry Vacuum Industry Processing details Machining Center, Tig Welding
Production process
Connect with Our Dedicated Team
We can handle a wide range of services from technical consultation on product production and processing to consultation on specific estimates.
Liquid Cold Plates by FSW(Friction Stir Welding)
Advantage 1: Uniform Cooling Performance
In order to make the lid thickness uniform after the surface finishing process, as shown in the figure, a dedicated press machine is used to correct the warping and distortion of the base material and the lid. After that, the finishing process is carried out. A uniform lid thickness will be realized by this process. If the thickness of the lid is uniform, the distance from the groove (cooling channel) to the top surface of the lid (contact face) is also constant, and it has a cooling performance with no variation.
If the finishing process is done from the contact area without correction with a press machine, the thickness of the lid at the time of completion will change depending on the place as shown in the figure. If there is a thick part and a thin part of the lid with respect to the groove (cooling channel), a temperature difference will be created due to the difference in thickness, and as a result, the cooling performance will vary.
Advantage 2: High Joints Reliability
The joints by FSW can be made with the lid onto the base material closely without gaps.
In fusion welding by an electron beam that heats the material above the melting point temperature, there are concerns in the reliability of the joints due to slag and bubble. And in the brazing process, there are concerns about joint failure due to brazing shortage. On the other hand, FSW, which is a solid phase joining, is heated and softened as a solid without melting, and then pressurized to be joined. So there is almost no slags, air bubble and thus joining defects will rarely occur. Therefore, it has realized high reliability at the junction of the base material and the lid.
Advantage 3: High-Mix Low-Volume(HMLV) Production
The parts used in the manufacturing equipment in production line are different from the ones in mass-produced products, and equipment-specific customized ones are also required. Since FSW is used utilizing a dedicated processing equipment, it can be used for high-mix low-volume production.
Our processing equipment is a specially made hybrid machine that can perform cutting and joining (FSW) on the same machine. We have an integrated production system from machining to joining, and we can manufacture products that guarantee high quality.
Advantage 4: High Material Strength
FSW can maintain high material strength. In the case of brazing, the entire material will become hot during the brazing process and the base material will soften. In some cases, the more bend with own weight, the weaker the strength of the material becomes. On the other hand, FSW is a solid phase joining, and the base material does not soften because there is no need to heat the entire material. In addition, the joining part has a material strength equal to or greater than that of the base material. In this way, FSW is a joining method that does not reduce the material strength of the base material.
Connect with Our Dedicated Team
We can handle a wide range of services from technical consultation on product production and processing to consultation on specific estimates.
Things to consider when designing
1 Materials
Aluminum
Aluminum is excellent in terms of cost and weight. For example, the cost is about one-third in comparison to copper. In addition, it weighs only about one-third. On the other hand, compared to the thermal conductivity of copper 398W · m-1 · k-1, the thermal conductivity of aluminum is about half as much as 236W · m-1 · k-1. Although the cooling efficiency is inferior to copper, aluminum is suitable if you need a low-cost and lightweight cold plate.
Copper
The thermal conductivity of copper is 398W · m-1 · k-1, which is a high thermal conductivity compared to aluminum and stainless steel. For example, it is about 20 times that of stainless steel (SUS304) (16.7W · m-1 · k-1), and about twice that of aluminum (236W · m-1 · k-1). Therefore, if the heat dissipation performance is important, the use of copper is suitable.
Stainless steel
Stainless steel has high corrosion resistance. Compared to the use of copper or aluminum materials, an ion exchange unit is not required, and coolant (cooling water) management is easier. Therefore, if the maintainability of coolant is important, the use of stainless steel is suitable.
Temperature Uniformity
The cold plate doesn't just cool down. Depending on the location a uniform cooling function that does not vary is required. The cause of the cooling variation is the thickness of the lid of the groove in the cooling section. If the thickness of the lid varies from place to place, the temperature will vary and the function of the cold plate will decrease as you use it. In order to achieve uniform cooling properties, it is necessary to devise ways to keep the thickness of the lid constant and excellent processing technology to realize it.
Fluid(Coolant)
In general, a water-cooled cold plates determines the coolant (cooling water) that can be used depending on the material . Because if you do not choose the appropriate coolant, an electrochemical reaction causing corrosion of the material will occur between the material and the cooling water. For example, if it is aluminum, corrosion may occur even with chloride ions and copper ions contained in water. Therefore, it is suitable to use pure water managed by the ion exchange unit and antifreeze solution with rust inhibitor.
Joint Methods of Liquid Cold Plate's Production Process
Tube-in-Plate Type
It is a cold plate that embeds a cooling tube in the base material. Apply pressure to the pipe into the flow channel of the base material and insert it into the flow channel of the base material. It is difficult to create a complex flow channel because it is necessary to process pipes according to the flow channel. In addition, the pipe may not be able to follow the bending part of the flow channel, and there is a possibility that there will be a gap between the pipe and the base material, and the cooling performance may be reduced locally.
Brazing
Brazing is a method melting the adhesive called "brazing filler material" between the parts you want to join by heat and then fixing it with cooling. Unlike welding, the base material is not melted. There are several types of brazing fillers, and the one whose main component is silver is "silver brazing".
Brazing is possible both in the atmosphere and in vacuum, especially brazing in vacuum is possible to join with high airtightness, and there are many working examples in the cold plates. On the other hand, the heating of the brazing filler material and the heat treatment of the base material itself also occur, so there is a concern about the decrease in the strength of the base material due to the thermal effects.
FSW(Friction Stir Welding)
FSW stands for Friction Stir Welding in English. Friction Stir Welding is a method of connecting pressing parts materials with strong force while rotating cylindrical tools with protrusions at the tip. The protrusions of the tool are applied to the joint point between the joining parts materials and the main material is softened by the rotating friction heat, and at the same time, the surrounding area is plasticized by the rotation of the tool, and the components are integrated. It can be used in the atmosphere in general. The heat influence of the joining part can be minimized, and the generation of noise and dust can be reduced.
Connect with Our Dedicated Team
We can handle a wide range of services from technical consultation on product production and processing to consultation on specific estimates.
Types of LIquid Cold Plates
1. Tube-in-Plate Liquid Cold Plates
Tube-in-plate liquid cold plates are a type of cold plate design that utilizes tubes embedded within a thermally conductive base plate, typically made of materials such as aluminum, copper, or stainless steel. Coolant flows through these tubes, absorbing heat from the base plate and dissipating it as it circulates. This design is relatively simple and cost-effective, making it a popular choice for a wide range of applications.
One advantage of tube-in-plate cold plates is their ease of manufacturing, which can help keep costs low. They can also be customized to accommodate various tube materials, shapes, and configurations, depending on the specific thermal management requirements of the application. However, tube-in-plate cold plates may not provide the same level of thermal performance as more advanced designs, such as those using microchannels or jet impingement.
2. Friction Stir-Welded Liquid Cold Plates
Friction stir-welded liquid cold plates are a type of cold plate design that uses friction stir welding (FSW) to join two thermally conductive plates, forming a sealed channel for coolant flow. FSW is a solid-state welding process that produces high-quality, leak-free joints, making it an ideal method for creating liquid cold plates.
Friction stir-welded cold plates offer several advantages, including excellent thermal performance, a strong and reliable joint between the plates, and the ability to accommodate complex channel geometries. This design is suitable for a wide range of applications, including high-performance electronics cooling, automotive battery cooling, and aerospace thermal management systems.
Shapes of LIquid Cold Plates
Liquid cold plates can be classified based on their shape, which can have a significant impact on their cooling performance and suitability for specific applications. Here are some common liquid cold plate shapes, along with their advantages, disadvantages, and typical use cases.
1. Flat Liquid Cold Plates
Flat liquid cold plates are the most common and versatile type of cold plate design. They consist of a flat, thermally conductive base plate with integrated coolant channels or tubes. Flat cold plates are used to provide direct contact with the heat source, ensuring efficient heat transfer and even cooling across the surface.
Advantages of flat liquid cold plates include their simplicity, ease of manufacturing, and compatibility with a wide range of applications. They can be customized with various materials, channel designs, and surface finishes to optimize thermal performance and meet specific requirements. However, flat cold plates may not provide the most efficient cooling for irregularly shaped components or in applications where space constraints demand more compact solutions.
Flat liquid cold plates are commonly used in electronics cooling, automotive battery cooling, and industrial equipment cooling applications, among others.
2. Contoured Liquid Cold Plates
Contoured liquid cold plates are designed with a curved or shaped surface to match the profile of the heat source or the surrounding environment. This design enables better contact between the cold plate and the heat source, improving heat transfer and cooling performance. The primary advantage of contoured liquid cold plates is their ability to provide efficient cooling for irregularly shaped components or in applications with limited space. By conforming to the shape of the heat source, contoured cold plates can minimize air gaps and ensure uniform cooling across the surface. However, they can be more complex and expensive to manufacture compared to flat cold plates, as they require specialized tooling and fabrication techniques. Contoured liquid cold plates are often used in applications such as cooling high-power LEDs, power electronics, and aerospace components, where irregular shapes and space constraints are common.
3. Enclosed Liquid Cold Plates
Enclosed liquid cold plates are designed with a fully enclosed structure, providing a sealed environment for the heat source and coolant. This design helps to prevent coolant leakage and contamination while ensuring efficient heat transfer within the enclosed space.
Enclosed liquid cold plates offer several advantages, including excellent thermal performance, protection from external contaminants, and compatibility with various coolant types. They are particularly well-suited for applications where the heat source must be isolated from the surrounding environment, such as in semiconductor processing or medical equipment cooling. However, enclosed cold plates can be more complex and expensive to manufacture compared to other designs, as they require precision machining and sealing techniques.
Enclosed liquid cold plates are commonly used in applications where the heat source needs to be isolated from the environment, such as semiconductor manufacturing equipment, medical devices, and certain high-performance electronics cooling systems.
4. Modular Liquid Cold Plates
Modular liquid cold plates are designed with a modular structure, allowing for easy integration and expansion of the cooling system. They consist of multiple, interchangeable cold plate modules that can be connected together to create a customized cooling solution.
The primary advantage of modular liquid cold plates is their flexibility, which enables users to adapt and scale their cooling systems as needed. Modular cold plates can be easily reconfigured or expanded to accommodate changes in the heat source, cooling requirements, or system layout. However, they may be more complex and expensive to manufacture and assemble compared to other designs.
Modular liquid cold plates are often used in applications where the cooling system needs to be easily adaptable or expandable, such as in data center cooling, large-scale electronics cooling, or high-performance computing systems.
Connect with Our Dedicated Team
We can handle a wide range of services from technical consultation on product production and processing to consultation on specific estimates.