Aluminum Cold Plates
What are Aluminum Cold Plates?
Aluminum cold plates are advanced thermal management solutions designed for efficient cooling of various components and systems. These cold plates are manufactured using aluminum, a lightweight and affordable material known for its good thermal conductivity and heat transfer properties.
Aluminum cold plates are engineered to transfer heat from the source to a coolant, which can be liquid or air, ensuring optimal temperature regulation and reliable operation of components. They are widely used across various industries, including automotive, aerospace, electronics, and industrial equipment cooling.
Production range
Material | Aluminum, Stainless steel, Copper |
---|---|
Joining methods | Tig welding, Vacuum brazing, Electron beam welding (EBW), Friction stirring welding (FSW) |
Maximum size that can be manufactured | Circular form:φ800mm Rectangular form:Width 1,000 mm、Length 2,000 mm |
Structure | The jacket structure having grooves covering the lid from the above is main. |
Shape | Compatible with various external shapes and complex waterway shapes |
Specifications | All manufactured parts are custom-made with customer specifications |
Product examples
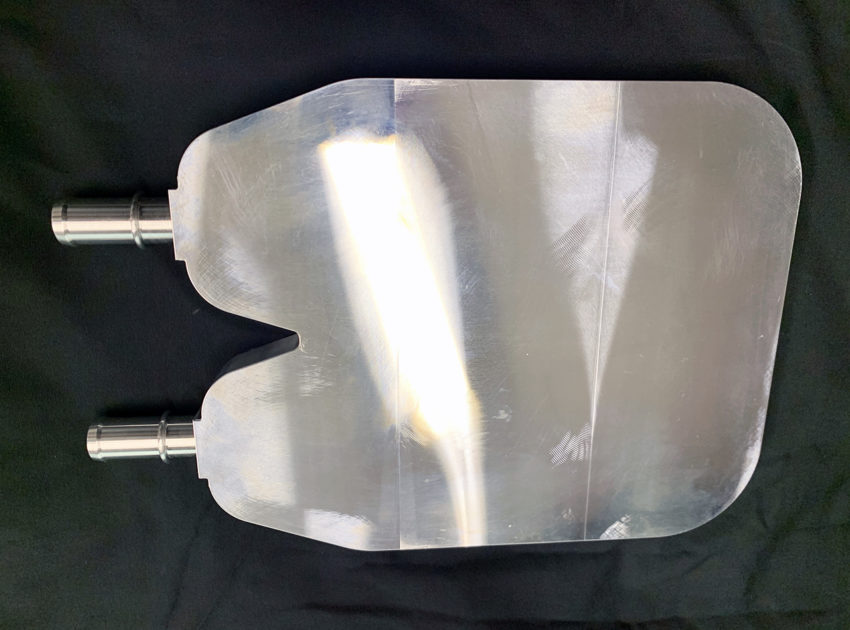
Aluminum Cold Plate
This case is a prototype development product that has been requested through the homepage. The water-cooled groove is processed into the main body, the lid is attached from the top, and then joined by FSW After joining with frictional stirring welding, the surface in contact with the heat source provides plane accuracy by machining The ...
Connect with Our Dedicated Team
We can handle a wide range of services from technical consultation on product production and processing to consultation on specific estimates.
Procution Process
Product | Customized Liquid Cold plate |
---|---|
Material | Aluminum (A6061) |
Processing method | Friction stir welding (FSW), Machining center |
Process❶ Water cooling groove machining and Fitting step processing on the lid
Using a machining center, water cooling groove processing (groove through which cooling water flows) is performed on the main body plate.
After that, fitting step processing on the lid is carried out (step-machining to fit in the lid).
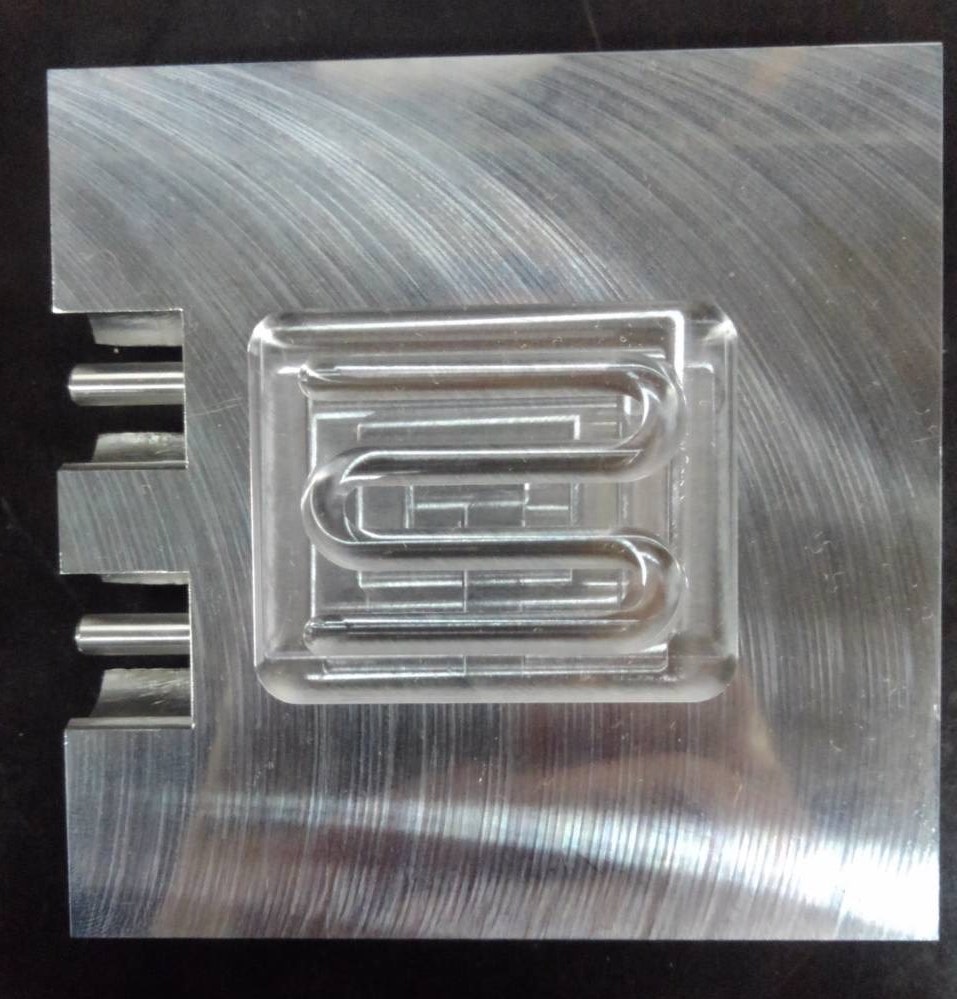
Process❷ Knock the lid
Knock the lid into the processed fitting step.
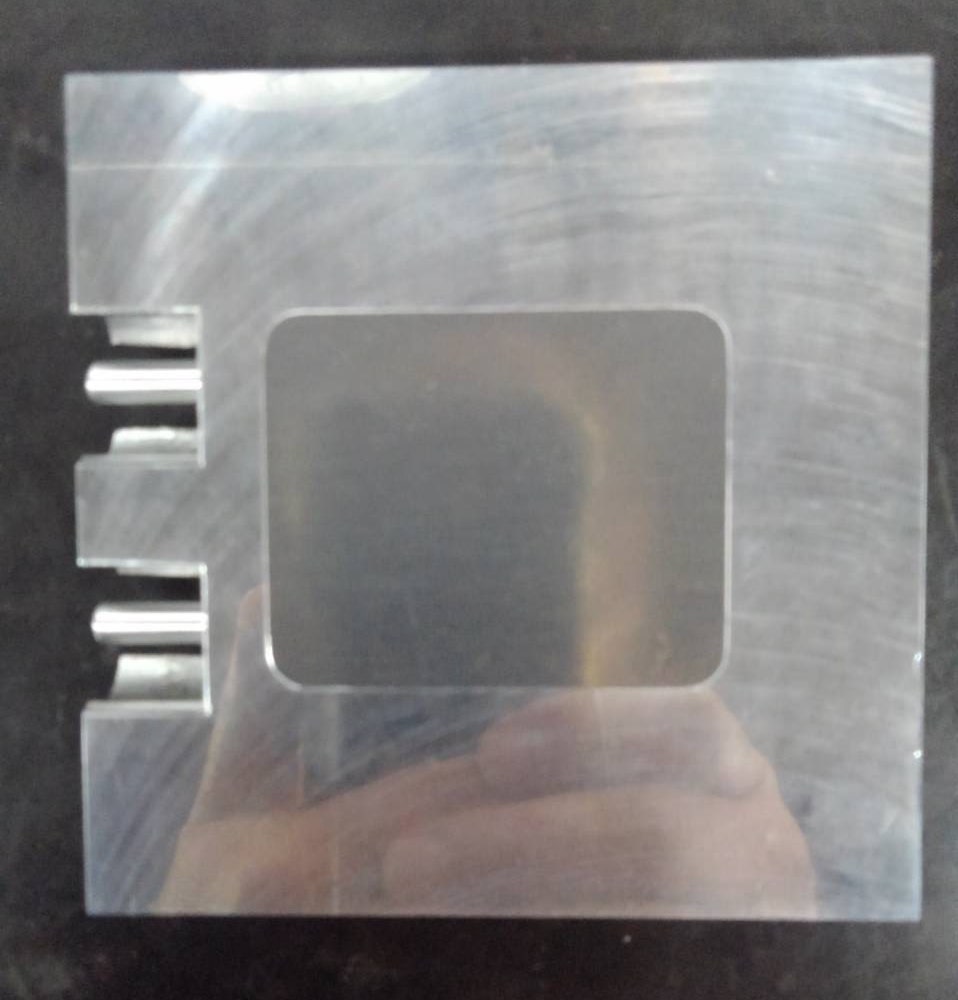
Process❸ FSW bonding
FSW junctions between the outer periphery of the lid and the water-cooled groove.
FSW bonding improves adhesion between the lid and the stepped surface.
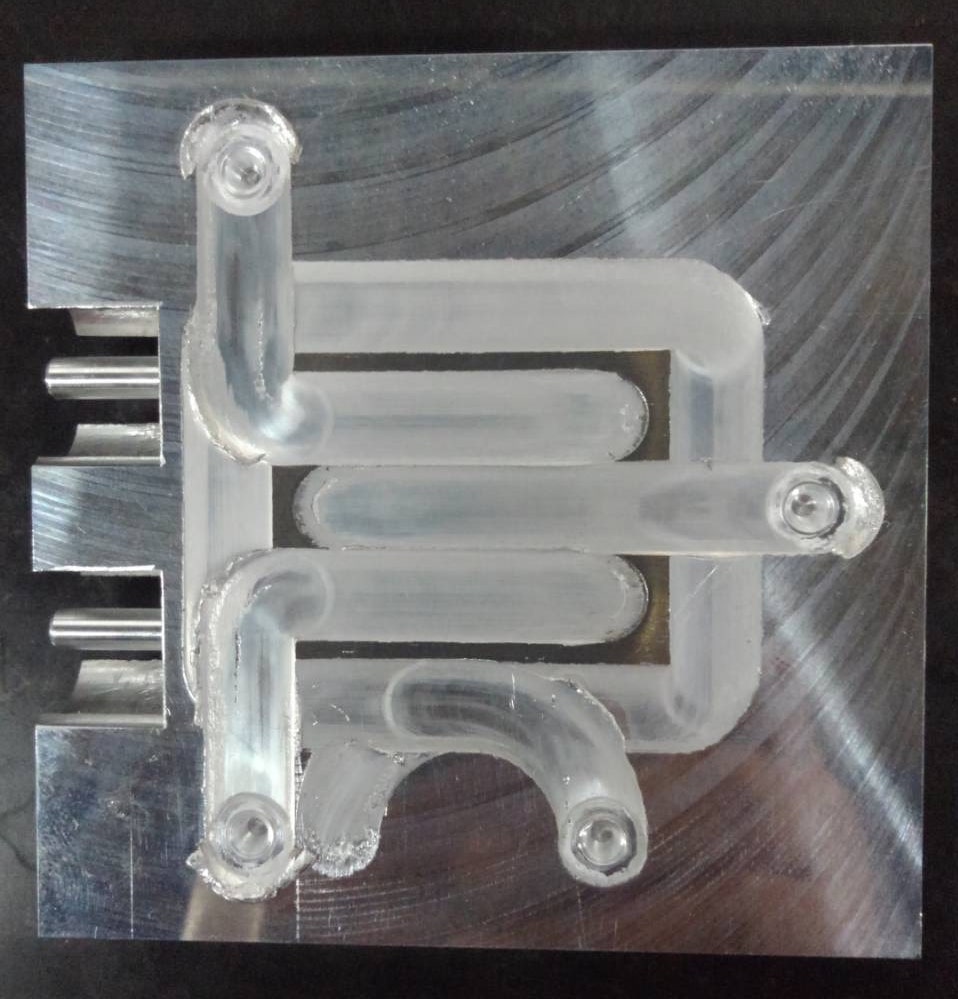
Process❹ Finish cutting
Cut the outer periphery and FSW joint surface at the machining center.
This ensures the plane accuracy of the joint face.
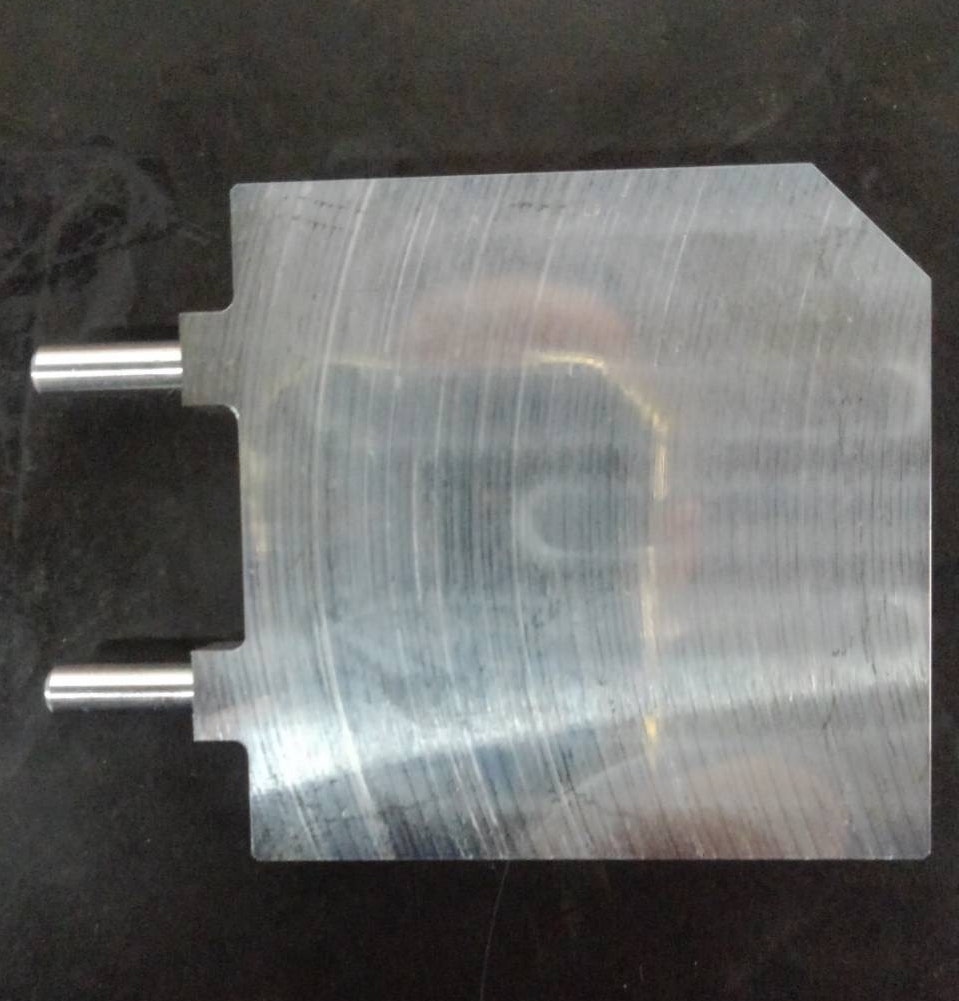
Aluminum Grades and Alloys for Cold Plates
Different aluminum grades and alloys are used in the manufacturing of cold plates, each offering distinct properties and advantages:
6061 Aluminum Alloy
This versatile and widely used aluminum alloy offers a good balance of strength, weldability, and corrosion resistance. It is commonly used in the production of aluminum cold plates due to its excellent thermal conductivity, mechanical strength, and overall performance.
5052 Aluminum Alloy
This alloy is known for its excellent corrosion resistance, particularly in marine environments, and good formability. It offers slightly lower thermal conductivity than 6061 but is still suitable for many cooling applications. 5052 aluminum alloy is ideal for cold plates used in corrosive environments or those requiring high levels of corrosion resistance.
Advantages and Benefits
Lightweight and Cost-Effective
Aluminum cold plates offer several advantages and benefits, making them a popular choice for many thermal management applications. One of the primary benefits of aluminum cold plates is their lightweight nature, which makes them ideal for applications where weight reduction is crucial. Additionally, aluminum is more affordable than other materials, such as copper or stainless steel, which makes aluminum cold plates a cost-effective solution for many projects.
Thermal Conductivity and Cooling Performance
Furthermore, aluminum cold plates exhibit good thermal conductivity, allowing for efficient heat transfer and cooling performance. Although not as thermally conductive as copper, aluminum is often sufficient for many cooling applications.
Corrosion Resistance and Durability
Aluminum cold plates are also known for their corrosion resistance, which contributes to their durability and long service life.
Customization Options
These cold plates can be customized to meet specific design requirements and performance objectives, such as optimizing the geometry and dimensions for improved heat dissipation or incorporating specialized coolant flow paths.
Comparing Aluminum Cold Plates with Other Materials
Aluminum cold plates are often compared to other materials, such as copper and stainless steel, each with its unique set of advantages and disadvantages:
Copper Cold Plates
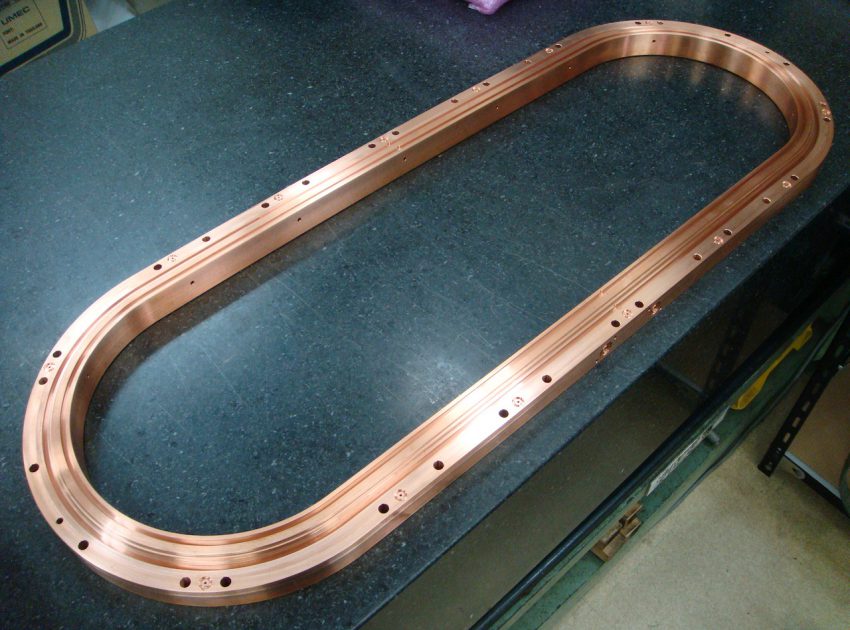
Copper cold plates offer superior thermal conductivity compared to aluminum cold plates, making them ideal for high-performance cooling applications. However, copper cold plates are typically heavier and more expensive than their aluminum counterparts.
Stainless Steel Cold Plates
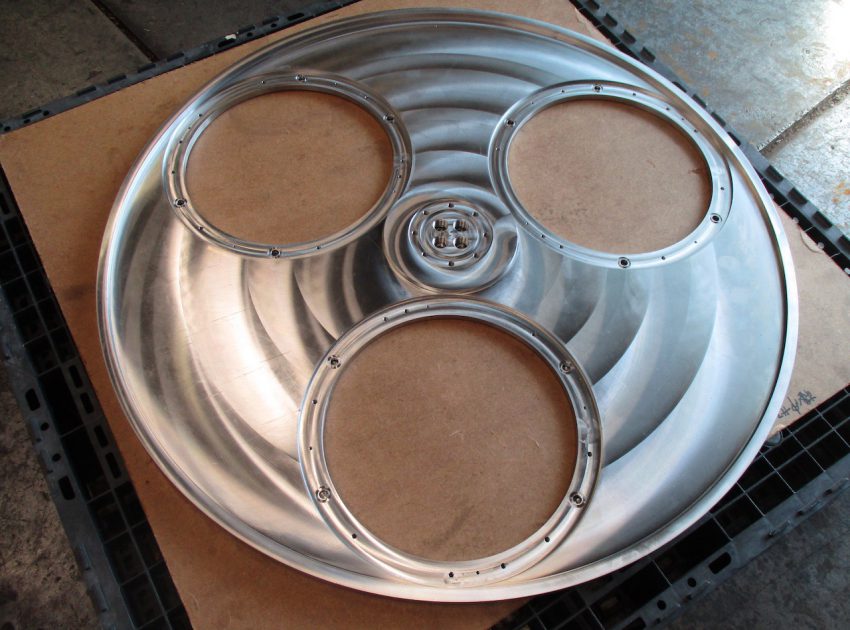
Stainless steel cold plates provide excellent corrosion resistance but have lower thermal conductivity compared to aluminum cold plates. While stainless steel is suitable for applications that require exceptional resistance to corrosion and chemical attack, it may not be the best choice for applications where high heat transfer performance is crucial.
Connect with Our Dedicated Team
We can handle a wide range of services from technical consultation on product production and processing to consultation on specific estimates.
Applications of Aluminum Cold Plates
Aluminum cold plates are used in a wide range of applications across various industries
Electric Vehicle Battery Cooling
Aluminum cold plates play a crucial role in the thermal management of electric vehicle batteries. They help maintain optimal operating temperatures, prolonging battery life and enhancing overall performance.
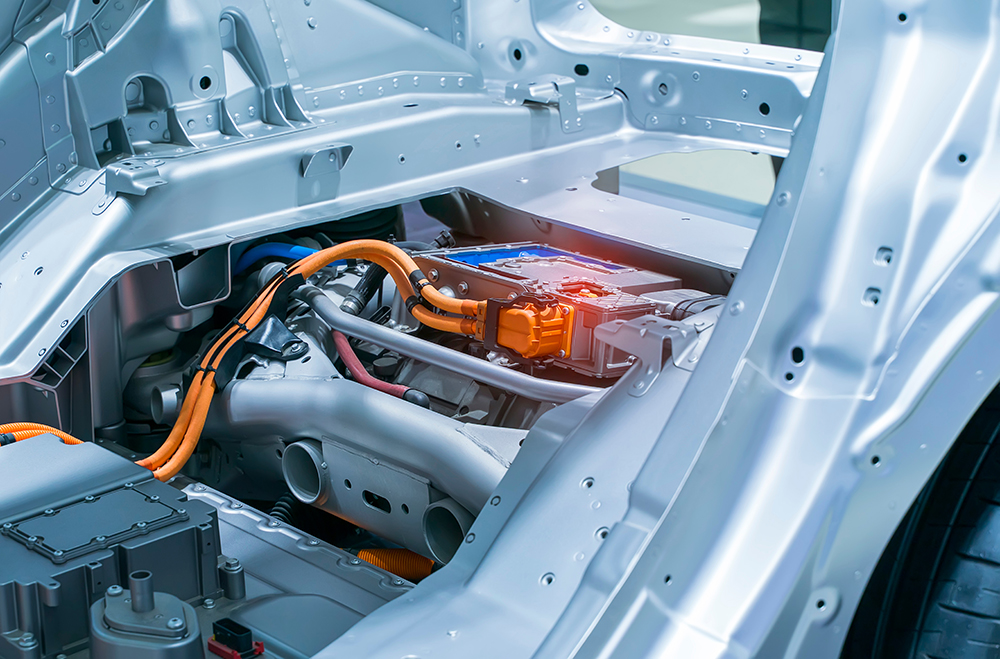
Aerospace and Defense Applications
In aerospace and defense systems, aluminum cold plates are employed for cooling critical components, avionics, and other heat-sensitive equipment. Their lightweight nature and corrosion resistance make them an ideal choice for these demanding applications.
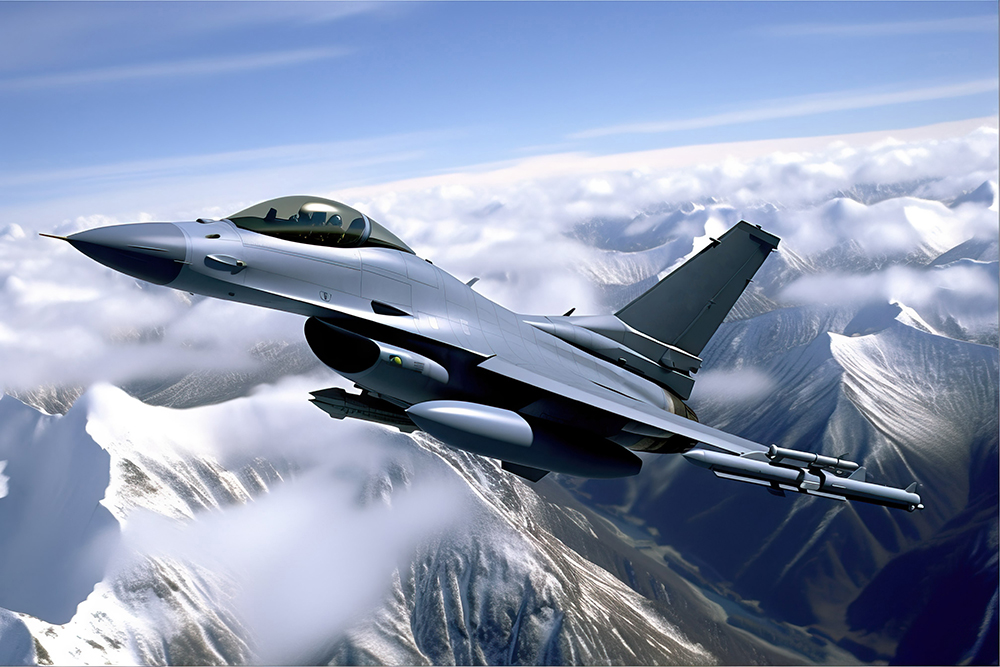
Industrial Equipment Cooling
Aluminum cold plates are also used in various industrial applications, such as cooling power electronics, laser systems, and hydraulic equipment. By providing efficient heat dissipation, aluminum cold plates contribute to the performance and service life of these essential industrial systems.
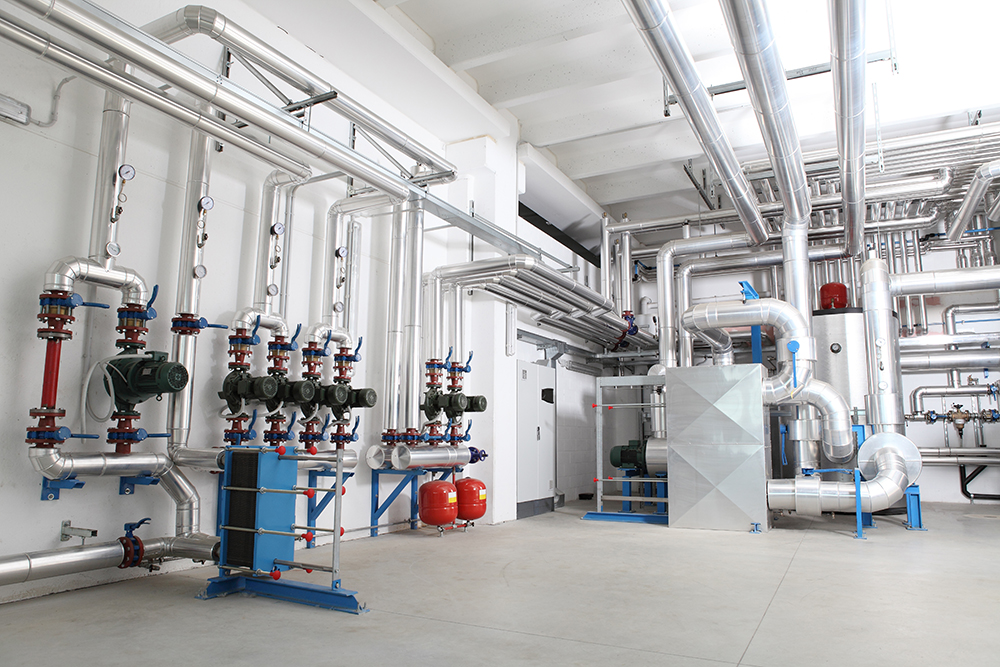
Connect with Our Dedicated Team
We can handle a wide range of services from technical consultation on product production and processing to consultation on specific estimates.
FAQs about Aluminum Cold Plate
How do aluminum cold plates compare to copper cold plates in terms of thermal conductivity?
While aluminum cold plates offer good thermal conductivity, they do not match the superior heat transfer performance of copper cold plates. Copper has nearly twice the thermal conductivity of aluminum, making it the preferred material for high-performance cooling applications. However, aluminum cold plates are still suitable for many applications, particularly when weight and cost are more important considerations.
Can aluminum cold plates be customized for specific applications?
Yes, aluminum cold plates can be customized to meet specific design requirements and performance objectives. Customization options may include optimizing the geometry and dimensions of the cold plate for enhanced heat dissipation, incorporating specialized coolant flow paths, or integrating mounting features to facilitate installation. By working closely with manufacturers and suppliers, engineers can develop customized aluminum cold plate solutions that meet the unique needs of their applications.
How do aluminum cold plates perform in corrosive environments?
Aluminum cold plates generally exhibit good corrosion resistance, making them suitable for use in various environments. However, certain aluminum alloys, such as 5052, provide even better corrosion resistance, particularly in marine environments or those with specific chemical exposures. In highly corrosive environments, additional protective measures, such as surface treatments or coatings, may be required to further enhance the corrosion resistance of aluminum cold plates.
Are aluminum cold plates suitable for high-temperature applications?
Aluminum cold plates are suitable for many high-temperature applications, but their performance may be limited by the material's melting point and thermal expansion properties. For very high-temperature applications, alternative materials such as copper or stainless steel may be more appropriate. It is essential to consult with cold plate manufacturers and experts to determine the most suitable material and design for high-temperature applications.
Connect with Our Dedicated Team
We can handle a wide range of services from technical consultation on product production and processing to consultation on specific estimates.