What is backing plates?
In thin film manufacturing of Liquid Crystal Panels and Semiconductors, a method of sputtering evaporates the metal and generates a circuit. The metal (target material) that evaporates when sputtering is very hot, so it cools and proceeds with the production process.
The backing plate is used to cool the target material.
The backing plate is used in the vacuum chamber of the sputtering device, and the material is made of copper and has a water-cooled jacket structure.
Our backing plates
The water-cooled jacket is formed by joining the main body and the water-cooled lid with vacuum brazing, electron beam welding, Friction Stirring Welding, etc.
In particular, Friction Stirring Welding system of our own facility is considered to be more reliable at the junction than melt welding when it comes to bonding nonferrous metals, and is actually used for bonding the bodies of aircraft and Shinkansen trains.
Kyoyu’s backing plates respond to various types of shapes ranging from round to angular shapes, and advanced distortion correction technology enables surface cutting after welding to maintain a constant thickness of the water-cooled lid, contributing to improved cooling efficiency.
Production range
Material | Aluminum, Stainless steel, Copper |
---|---|
Joining methods | Tig welding, Vacuum brazing, Electron beam welding (EBW), Friction stirring welding (FSW) |
Maximum size that can be manufactured | Circular form:φ800mm Rectangular form:Width 1,000 mm、Length 2,000 mm |
Structure | The jacket structure having grooves covering the lid from the above is main. |
Shape | Compatible with various external shapes and complex waterway shapes |
Specifications | All manufactured parts are custom-made with customer specifications |
Notes | We do not provide purchasing, sales, or bonding services for target materials. |
Production examples
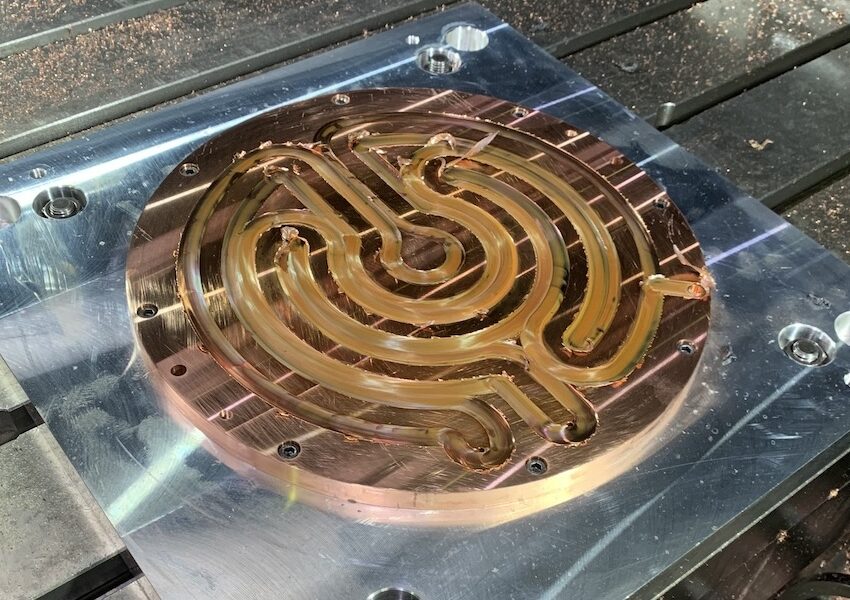
Sputtering Copper Backing Plate (Circular type)
This product has been requested through homepage. Surface of bonding-target is flat by 0.05. Material Copper Size Thickness 15 x Outer Diameter φ370 Industry Semiconductor Processing details Machinig-center,Lathe ,FSW
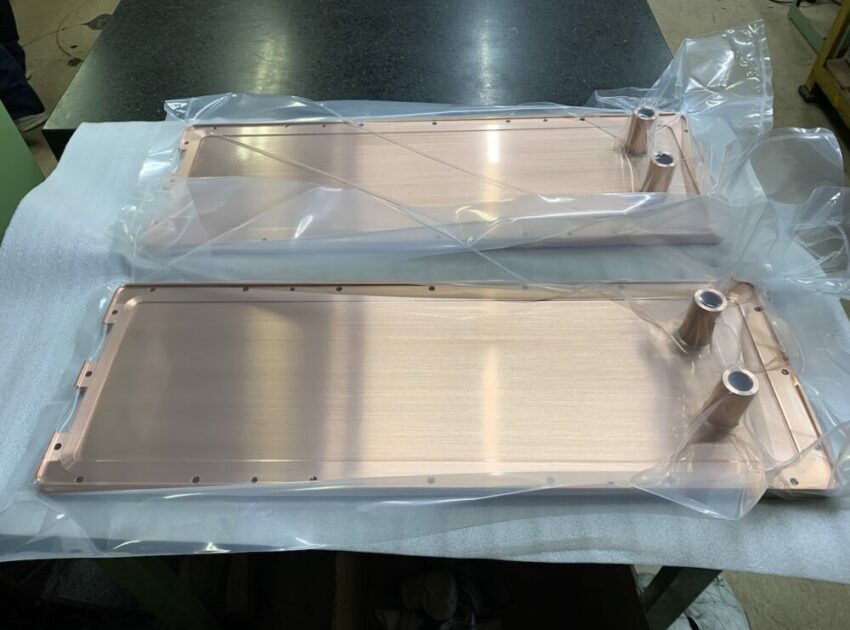
Pure Copper Backing Plate for Display Industry
This case shows one of products ordered by an overseas display manufacturer through the website. Product Name Backing plates Materials Pure copper (C1020) Size Width: 241 mm, Length: 691 mm, Thickness: 17 mm Industry/Field Displays Methods Machining center, FSW
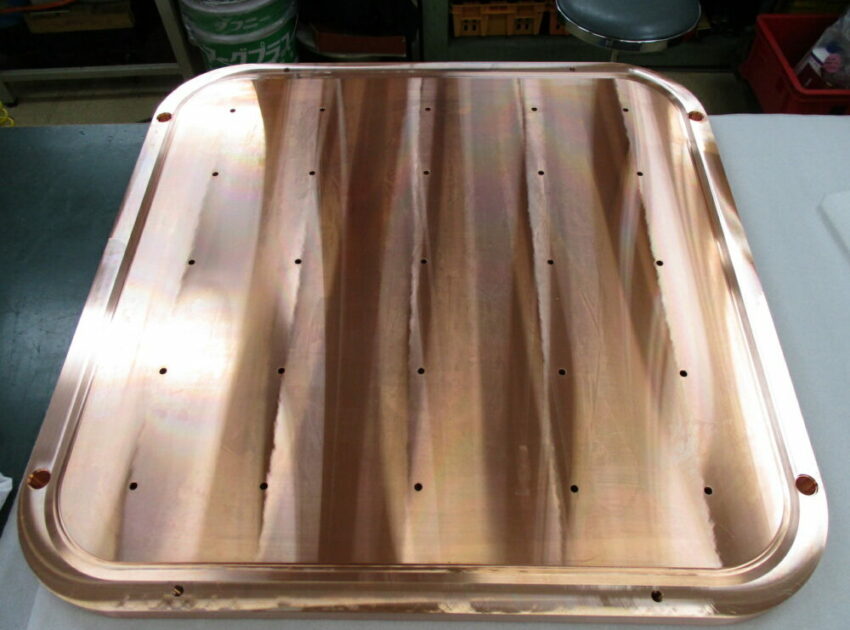
Pure Copper Backing Plate (Square shape)
This case is a prototype development product requested through the website. Materials Pure Copper(C1020) Size Width: 732 mm, Length: 732 mm, Thickness: 30 mm Industry/Field Semiconductors, Displays Methods Machining Center, Electron Beam Welding, FSW
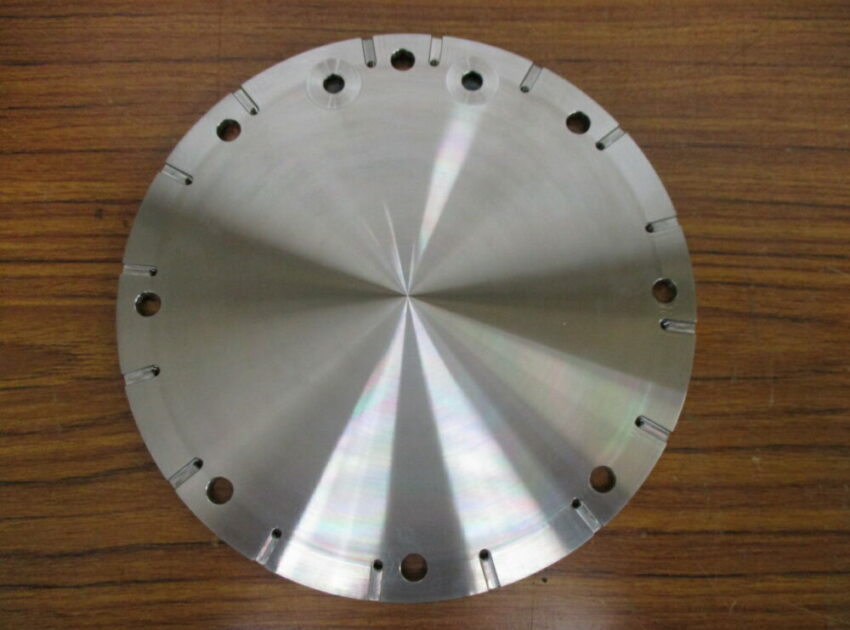
Stainless Steel Backing Plate (Circular shape)
This case is a prototype development product requested through the website. Materials Stainless steel (SUS304) Size Outer diameter: 220 mm, thickness: 8 mm Industry/Field Semiconductors, Displays Methods Machining Center, NC Lathe, TIG Welding
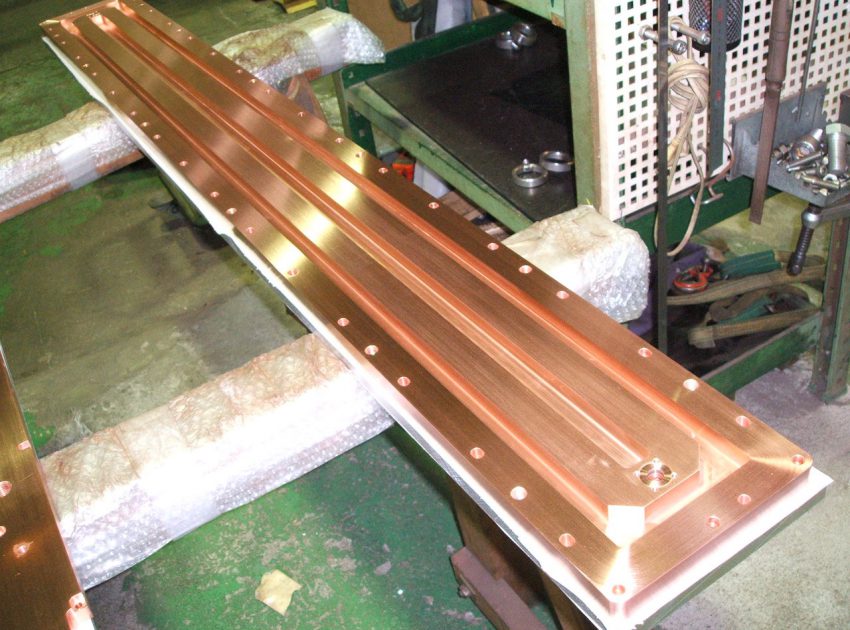
Pure Copper Backing Plate (Rectangular type)
Pure copper is a difficult material, and warping occurs after cutting or joining. Therefore, in order to ensure the thickness of the water-cooled lid, distortion correction is necessary each time. It is also easy to scratch, so you need to pay close attention. Material SUS304 , SUS316 Size W200mm~400mm x L500mm~1500mm Industry Vacuum Industry Processing ...
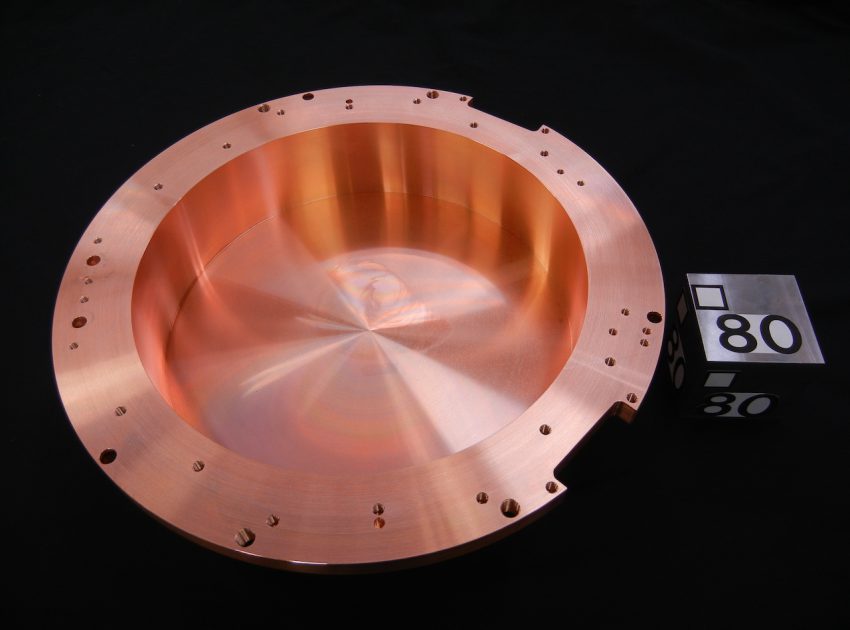
Pure Copper Backing Plate (Round shape)
Pure copper is a difficult material, and warping occurs after cutting or joining. Therefore, in order to ensure the thickness of the water-cooled lid, distortion correction is necessary each time.It is also easy to scratch, so you need to pay close attention. Material Pure Copper C1020 Size Around 500mm in dia Industry Vacuum Industry Processing ...
FAQs about Custom-made Backing Plates Manufacturing
Is it possible to request the production of only backing plates that do not bond the target?
We do not support target bonding processing (customer handled), but specialize in backing plate production (cutting and joining).
We receive a wide range of requests from equipment manufacturers, target manufacturers, and device manufacturers who need a backing plate only.
Is the square shape backing plate the only shape that can be supported?
Based on customer specifications, we can handle whichever both round and square shapes. In general, it is a round shape for semiconductors and a square shape for displays.
Is copper the only material that can be used?
Accordint to the customer's application and specification, we can handle whichever copper, aluminum and stainless steel.
How to join the cooling structure and the water cooling lid and what merits do you have in comparrison to other companies?
The cooling structure is mainly a water-cooled jacket type in which a groove is processed into the main body that serves as a flow path and put the lid over the groove.
Joining methods include TIG welding for stainless steel, FSW (friction stir welding), vacuum brazing, and electron beam welding for copper and aluminum.
In particular, TIG welding and FSW (friction stir welding) can be produced in an integrated manner with our own equipment, so we believe that there is an advantage in terms of price and delivery time.
After joining the water-cooled lid, the main body plate is distorted, and if the joint surface is cut in that state, the thickness of the lid will vary, but what are the countermeasures?
If distortion occurs such as bending of the main body plate, the distortion is removed by our own hydraulic press, and after ensuring flatness, the joint surface is cut, so variations in the thickness of the water-cooled lid are minimized.
First, please feel free to contact us.
We can handle a wide range of services from technical consultation on product production and processing to consultation on specific estimates.
Things to consider when designing
1 Materials
Aluminum
The cost of aluminum is low that is about one-third of copper. The thermal conductivity shows a good value although it is about half compared to 236W · m-1 · k-1 and copper 398W · m-1 · k-1. On the other hand, Young's modulus is about 70GPa, which is low and easy to deform compared to about 115GPa in copper and 196GPa in stainless steel. Therefore, if the usage environment with a relatively low load on the backing plate or if the heat generation is relatively low as low as copper, it can be produced at a low cost.
Material | Young's modulus in ksi |
---|---|
C10100(OEE copper) | 16700 |
C11000(ETP copper) | 16700 |
C18200 Chromium copper | 18900 |
Molybdenum | 47700 |
304 Stainless Steel | 28500 |
6061 Aluminium | 10000 |
*1ksi=6.8965517241379MPa
Copper
The copper backing plate using oxygen-free copper (C1020), which has the lowest oxygen content among pure copper is a mainstream. As for Tough- pitch copper materials, there are some concerns of generating gases in a vacuum environment. The thermal conductivity of copper has a high value of 398W · m-1 · k-1, and it is a relatively easy material to process. Copper materials are suitable for places where high heat dissipation is required or when complex processing is required. The Young's modulus is also about 115GPa, which is high in strength and hard to deform. On the other hand, due to pure copper being a difficult-to-cut material, it is a material that requires high processing technology.
Stainless steel
Stainless steel has a thermal conductivity of 17W · m-1 · k-1 and that is not so good compared to copper but the Young's modulus is 196GPa , which is higher than about 115GPa for copper.
On the other hand, it is not suitable for complex shapes and/or fine shapes due to poor processability.
2 Thermal Conductivity
During the sputtering process, the surface of the sputtering target will be hot, so the heat generated must be continued to be cooled. Therefore, backing plates are required to be made of materials with high thermal conductivity in order to efficiently cool the heat generated on the backing plate
In addition, if there is a temperature difference between the sputtering target and the backing plate, thermal stress will be generated, and cracks and peeling will occur with brittle materials, so it is also important to use materials with high thermal conductivity to equalize them.
Generally, thermal conductivity is material-specific, so if you want high cooling efficiency, a material with high thermal conductivity will be chosen.
3 Mechanical Strength
The backing plate also requires mechanical strength. There are two types of cooling methods for the backing plate in sputtering, a direct method to cool the backing plate itself and an indirect method that cools the device and cools it by heat conduction.
In the case of the direct method, high pressure is applied to the backing plate, which can cause the backing plate to warp and at the same time, warping, cracking and peeling of the sputtering target on the backing plate may occur.
Therefore, the backing plate requires a high strength (Young's modulus) that is difficult to deform even if high pressure occurs. Since the Young's modulus is material-specific, if you want to minimize the warping caused by cooling, you will choose a material with a high Young's modulus.
Types of Backing Plates
Jacket Water Cooling Type
The jacket-shaped backing plate is divided into a base part and a lid. A part of the base part is formed with grooves through where cooling water flows . The waterway of the base part is covered by the lid. The base part material and the lid are joined by brazing or friction stir welding, etc.
One Body Type
The sputtering target and integrated backing plate are manufactured with the same material as the sputtering target and backing plate. Since it is integrated, it has the advantage of reducing the target's replacement time as much as possible and the manufacturing costs can be reduced. On the other hand, because it is an integrated type, there is also a concern about warping during sputtering due to lack of strength.
Process of Backing plates fabrication
STEP 1: Forming Groove
Process a pocket-shaped groove that receives a lid on the base part. A groove that is the passage of cooling water is created in this groove by cutting process.
STEP 2: Manufacturing a Lid
Separately, make a lid to cover the pocket-shaped groove .
STEP 3: Join the Lid
Join the base and the lid.Fit into a pocket-shaped groove. After that, the base and the lid are joined using one of the joining methods such as electron beam welding, brazing, or friction stir welding.
STEP 4: Finishing
Finish the surface of the joint face of the base and the lid. Since unevenness and distortion occur during joining, the joint surface is finished smoothly by cutting process.
First, please feel free to contact us.
We can handle a wide range of services from technical consultation on product production and processing to consultation on specific estimates.